Implementation of workplace safety management policy
Internal Organization and Environmental, Health, and Safety Principles
Advantech is a global citizen that upholds the corporate objective of providing people with fulfilling lives. In addition to complying with occupational health and safety related regulations and other relevant requirements, the Company also pays attention to important global OHS issues, hoping that all employees can grow safely in a friendly environment. Consequently, the Company has established an occupational health and safety management system in a bid to foster a safe and healthy workplace, prevent unsafe conduct, minimize occupational disasters, and ensure that employees can enjoy work and lead healthy lives.
Occupational health and safety management system (ISO 45001:2018)
Advantech has obtained ISO 45001 certificates from third-party certification firms for the headquarters, Advantech China, and Advantech USA. Furthermore, it has formulated the “Occupational health and safety policy”. The OHS policy is approved and decided by the board of directors of Advantech and implement the decision and announce it on the official website. The OHS management system covers both Advantech employees and non-employees. The Company adopted a hierarchical and parallel structure extending from top to bottom to various Occupational Health and Safety personnel in different regions. Adhering to the ISO 45001 management system and establish the OHS program, these personnel were responsible for planning, promoting, supervising, and auditing the operation of the system. Management synergy is achieved through procedural document control, regular follow-up management, and compliance with the PDCA approach. The OHS management system was reviewed and adjusted on a rolling basis during the period to reinforce employees‘ awareness of self-protection. This not only reduces workplace risks but also prevents occupational accidents, thereby ensuring employee safety and health. Although other regions are not the main production regions, the Company is still actively planning to progressively implement ISO 45001 system management.
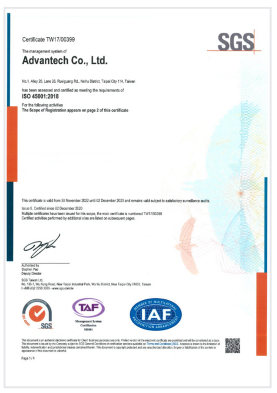
Occupational Health and Safety Education and Training
The concept of sustainable business operation and compliance with occupational safety and health laws and regulations are implemented to ensure the validity of the certificates of the executive personnel of the occupational safety and health management system. Regarding internal occupational safety and health education and training for new recruits and incumbents, each factory plans to conduct annual safety education training courses. The content of the courses includes organic solvent operations, operation of mechanical equipment, 6S, fire drills, explosion-proof and other related courses.
Safety and Health Performance Indicators
To effectively promote the safety and health implementation plan, the safety and health performance indicators were set, and the implementation status was monitored. The headquarters regularly reported the progress of safety and health projects to the executive level supervisor, various organizational levels of the Company, and labor representatives through the occupational health and safety committee to achieve horizontal internal communication.
In 2023, Advantech China also formulated relevant safety and health indicators such as major environmental accident control, employee occupational disease control, work-related injury accident control, and emergency response implementation rate. Since Advantech USA is primarily an office area, key indicators include the bolstering of company-wide employee education and training (e.g., environmental safety, CPR, AED, etc.)
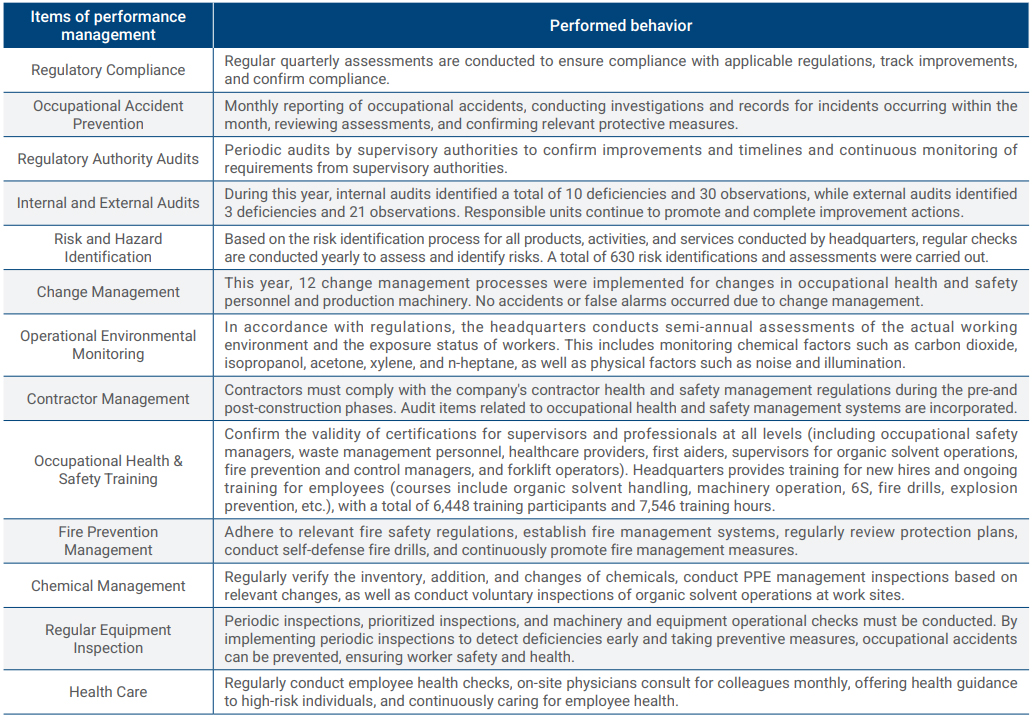
Occupational Hazard Identification and Risk Assessment
All safety and health aspects and workplace operational activities that interact with the Company's activities, products, and services are within the scope of hazard identification and risk assessment. Safety and health hazard identification and risk assessment are carried out by the identification team. Environmental and safety and health impact analysis is conducted based on the identification parameters, risk factors and risk assessments are calculated, and the assessment value levels are divided into 0, 1, and 2. "2" is the risk that should be handled, and needs to be controlled using the priority order, such as eliminating hazards, substitute with less hazardous materials or equipment, engineering control, administrative control, education and training, PPE, and emergency response. Advantech has formulated management plans to improve OHS performance, and set goals for monitoring, control, and improvements. In 2023, Advantech headquarters implemented 894 environmental/OHS risk items for newly purchased equipment, expansion of production lines, and regulatory changes. The risk assessment results revealed a low level of risk. To continuously optimize a friendly workplace, Advantech categorizes risk assessment values to ensure that aspects such as equipment functionality and other aspects related to the environment, safety, and health (ESH) meet the Company’s requirements and safety standards.
Besides promoting the safety and health obligations of employees, the importance of self-protection was also emphasized. In accordance with the criteria of "threat of imminent danger" in Article 18 of the Occupational Health and Safety Act and Article 25 of the Enforcement Rules of the Occupational Safety and Health Act, all employees are informed that if there is a threat of imminent danger on the job, apart from reporting it immediately, they may evacuate to a safe place and will not be disciplined by the Company. In 2023, there was no record of employees being disciplined for reporting safety hazards and evacuating to a safe location. For the reporting and grievance mechanism, see Figure 5.4.2 Whistleblowing and grievance mechanisms.
Incident notification and investigation procedures
Advantech strives to achieve the safety goal of "zero accidents in the workplace" and has established the "Job accident investigation and treating SOP" to regulate relevant procedures such as incident reporting, accident investigation responsibilities, subsequent improvement actions, and preventing similar accidents from occurring again.
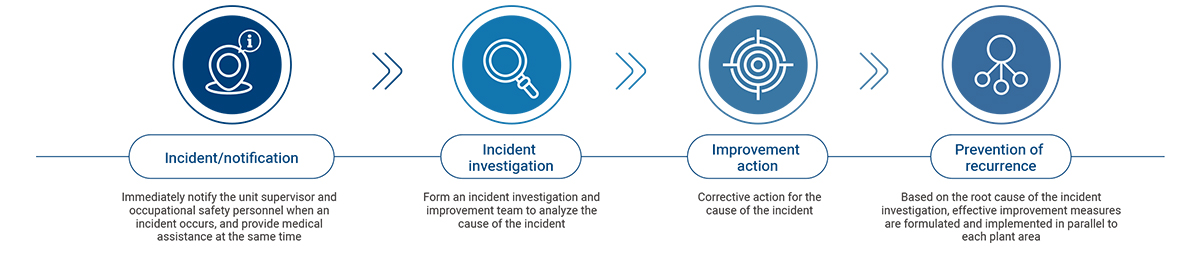
Disabling injury statistics analysis
Advantech aims to achieve "zero accidents in the workplace" and has established the "Job accident investigation and treating SOP" to regulate accident reporting, incident investigation responsibilities, investigation levels, procedures, and accountability. Following an accident, the group requires immediate reporting by on-site personnel and unit supervisors. Furthermore, unit supervisors, Occupational Health and Safety management personnel, and healthcare providers are tasked with investigating and handling the accident, as well as preparing an accident report.
Employee Absentee Rate Statistics
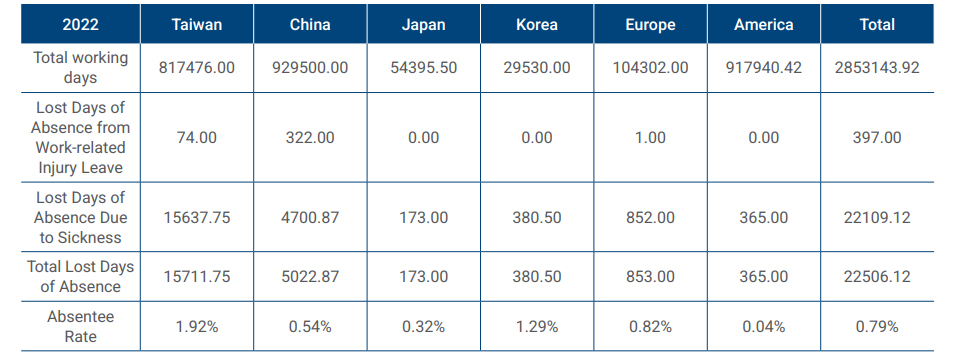
1. Absentee rate calculation method: (Total number of absent days [injury leave + sick leave + menstrual leave + pandemic leave]/total person-days) x 100%
2. The absentee rate target for 2023 is 0.9%. The absentee rate calculation includes occupational injury leave, sick leave, and menstrual leave. In 2023, Advantech saw a decrease in overall occupational injury leave through internal education, training, and enhanced awareness efforts. However, the provision of five days of paid sick leave and menstrual leave as employee benefits indirectly influences the overall absentee rate performance.
Occupational health and safety committee
Advantech headquarters (Taiwan) has established an occupational health and safety committee in accordance with the law, convening regular quarterly meetings. The Committee is composed of management and labor representatives, responsible for coordinating OHS-related affairs and promoting OHS management system development; Internal communication between all levels, relevant external units, and labor representatives to ensure a safe working environment for colleagues.
Intrinsic Safety
Each plant continuously injects resources into planning and creating a healthy workplace and cultivates a safety culture that puts people first to construct a work environment based on intrinsic safety. This promotes employees' physical and mental well-being, achieves work-life balance, and reduces safety hazards during operations, preventing accidents. This is accomplished through implementing control measures in mechanical equipment, emergency response and drills, workplace environmental monitoring, chemical control, hazard identification, and risk assessment, embodying the optimization of safety.
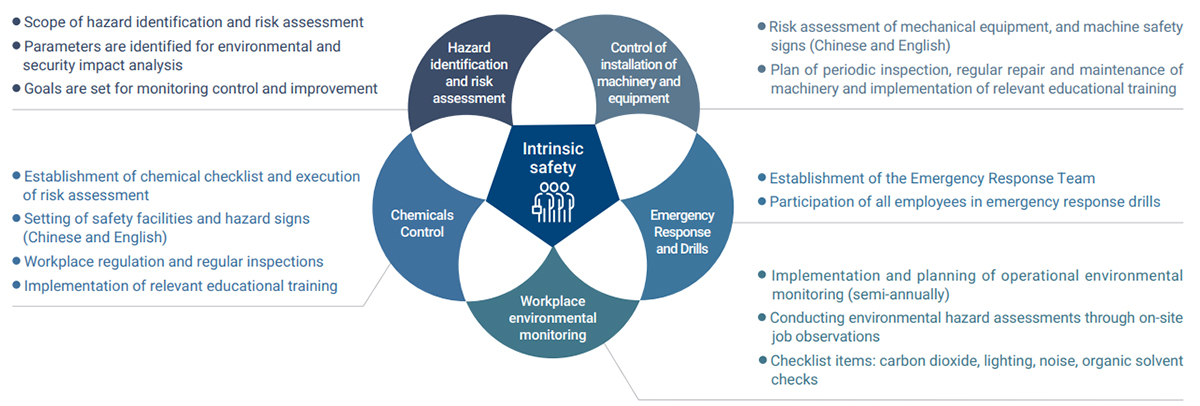